Concrete tie
We usher in brilliant future of domestic railway industry with our differentiated technologies.
Tie manufacturing process
(Prestressed Concrete Sleeper) KRS TR 0008-09R
The manufacturing process for our PSC Tie was established in conformity with the specifications of the Korea Railway Standards
and will be explained based on essential items of concerned specifications.
Concrete PSC manufacturing process flow chart
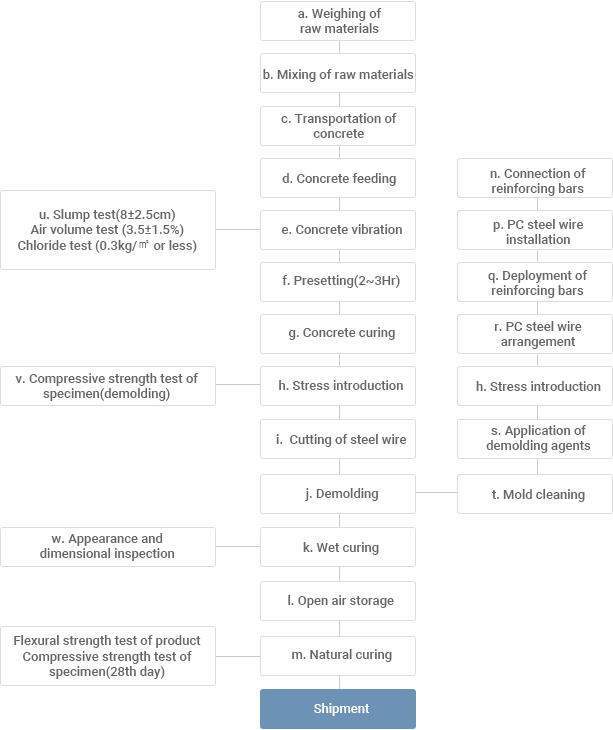
Weighing of concrete materials
Concrete material devices should be automated metering devices that are suitable for tie production and capable of metering within the metric errors set forth in concrete standard specifications.
- Metering devices for each material are automatic equipment fitted with electric load cell
Each device for metering the materials should be precisely calibrated by an accredited calibration laboratory prior to start of initial operation and should be calibrated periodically during the manufacturing process.
- We calibrate each metering device regularly at calibration laboratory and carry out inspection of the metering devices independently twice a year.
Concrete Mixing
Concrete mixing should be performed with a batch mixer. Mixing should be done sufficiently in such a way that the mixed concrete has moldability and uniform quality. Concrete mixing should be not performed for other purposes until the mixing is completed.
- As it is controlled automatically as automated plant, arbitrary control is impossible during the operation after inputting the test result values.
The mixer should be checked by the performance test under the KS F 2455 to make sure that it has the required mixing performance and that the materials are not separated during discharge of concrete.
- The mixing time should be set to at least 90 seconds.(set to proper value based on test)
The sequence of feeding the materials and mixing duration should be determined by the test. No water should be added separately.
- Sequence of feeding the materials: sand, gravel, cement, water (admixture should be fed in at the same time)
- Automatic surface water measurement device should be installed to maintain quality at constant level.
Mold cleaning and demolding agent application
Before applying the concrete, the inside of the mold should be cleaned and proper releasing agent should be applied to facilitate the demolding. During the demolding, be careful to prevent products from being scratched, cracked, or damaged.
- Mold cleaning should be cleaned first with dedicated cleaning device. The secondary cleaning should be performed manually. The third cleaning should ensure removal of concrete residues in molds.
- Heavy oil such as grease, etc., is used in molds. For the inside of the mold, water-based demolding oil for tie is used.
Installation of PS steel and tensile strength
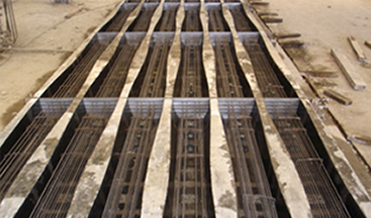
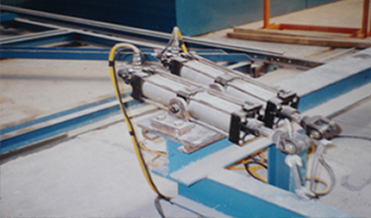
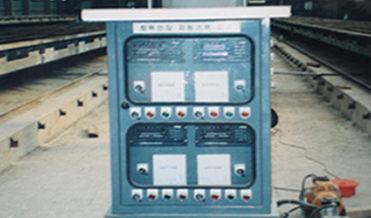
The PS steel should be tightened by placing a space to ensure placement in correct position as shown on the shop drawing, and the fixing device of the PS steel fixing part should be able to secure a firm fixing force to ensure that the prestressed concrete can be maintained constantly.
- Use a special arranger to mount the steel wire on the fixed end and tension end, secure the space by inserting the spacers between the molds, and make the spacers adhered closely to ensure that the mortar does not leak.
- After the arrangement of steel wire is completed, reinforcement bar should be placed. When the preliminary tensioning and main tensioning are completed, reinforcement bars should be connected to the positions specified in the shop drawing.
- Preliminary tensioning should be performed after individual tensioning by using individual tensioning device, so that same pressure can be applied by each strand.
After PS steel is pre-tensioned for at least 20 minutes in a range of 80% of the design load(initial tension) and released, main tensioning should be performed. The load of preliminary tensioning, main tensioning, etc., should be automatically recorded.
After main tensioning, the tensioning force of each steel wire should be checked in the presence of supervisor. The preliminary tensioning and main tensioning should be performed in the presence of supervisor of production and should be recorded.
- We have 2 units of 300-ton tensioning machines per bed. The results are recorded with automatic recording devices during the tensioning.
- A load of 3,120 KGF per strand should be applied.
- Check tensile strength per strand in the presence of supervisor by using the gauge(fitted with pressure cell) for checking individual tensioning.
Concrete Compaction
Concrete placement should be completed within 1 hour after mixing. During concrete placement, temperature of concrete should be within 10-30℃.
- The concrete is transferred to indoors throughout the section from mixer plant to placement location. The duration is about 90 seconds. No change occurs during the transfer.
Concrete compaction should be carried out by using the mold vibrator or vibration table or mechanical rod compaction, etc., which are suitable for the mixing characteristics and production facility system. The compaction equipment should be capable of sustaining the vibration with frequency suited for the mixing characteristics.
- Dedicated concrete feeder should be used to ensure uniform distribution of proper amount of concrete.
- The method adopted by our company uses the mold vibrator with high frequency of about RPM9000 for compaction with tight internal structure.
Sequence of feeding the materials and mixing duration should be determined by the test, and no water should be added separately.
- Frequency of feeding the materials: sand, gravel, cement, water (admixture should be fed in at the same time)
- With installation of automatic surface water measurement device, the quality can be maintained at a constant level.
Concrete Curing
Products that completed compaction should be immediately covered with a curing cover to avoid direct sunlight and drying of the surface, and should be protected in such a way so as to prevent sudden temperature changes.
- Remove the cover when initial set of concrete begins upon completion of concrete placement, and then put the cover.
After the concrete placement is completed, concrete should be cured by steam or heat after an elapse of at least 2 hours at room temperature. The rising rate of curing temperature should be 15 ℃ or less every hour. The descending rate of curing temperature shall be 10 ℃ or less every hour and not exceed 55 ℃.
- After putting the cover, the concrete should be fixed at room temperature for more than 2 hours before proceeding with curing by heat(automatic recording of curing graph).
- The rising temperature is kept at 15℃ or less every hour, and the descending temperature is kept at 10℃ or less. The maximum temperature is maintained at 55℃ or less.
The temperature detection devices should be able to measure the temperature anywhere inside the curing room, and the curing room should be equipped with automatic temperature recording and automatic temperature control system for each bed. Total steam curing time should be at least 12 hours.
- Automatic temperature control system should be put in place, and total steam curing time of at least 12 hours should be managed.
The boiler should be of sufficient capacity for proper temperature rise and maintenance, and the curing space should be equipped in such a way so as to prevent rapid temperature changes and local temperature differences.
- We have 2 boilers, each with a capacity of 2 tons/hour. The curing space uses the dedicated curing cover conforming to the Tie Specifications.
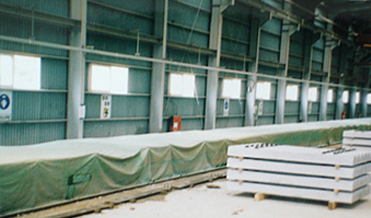
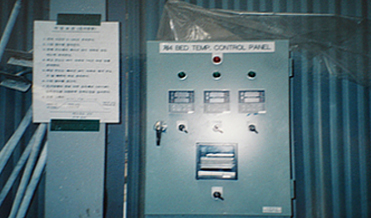
Introduction of prestress in PS steels
When prestress is introduced, the compressive strength of concrete should be 30Mpa or higher. The prestress should be slowly introduced at room temperature to reduce the impact inside the tie and the loss of prestress.
When prestress is introduced, it should be introduced on the same cross-section simultaneously to ensure that abnormal eccentric load, etc., do not occur on the cross-section of PC tie.
- The compressive strength is checked prior to introduction of prestress. The prestress is introduced on the same cross-section simultaneously.
Cutting of PS steel & finishing of the end
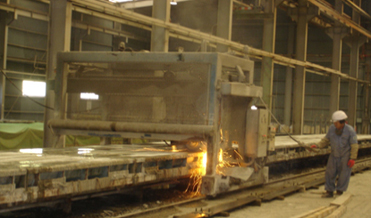
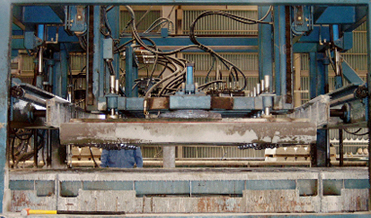
PS steels should be cut at right angles to the bottom of the tie so as to prevent any uneven prestress or any damage to PC tie end.
- Dedicated steel wire cutting machine is used to ensure proper cutting. (verification by dimensional inspection)
- Dedicated air compression type vacuum demolding machine, which has a structure preventing any damage to product, is used for demolding. Dedicated portable JIG is used for loading.
Product Curing
The Tie should be wet cured for at least 3 days in the room at the temperature of 5 ˚C or higher to ensure that its surface is not exposed to rapid temperature changes or drying, etc., after demolding. During the wet curing in winter, the Tie should not be exposed to external air before being air-dried.
- Wet curing is performed for 3 days in a dedicated space with spraying equipment capable of loading the maximum production quantity of 3 days. In winter, the temperature of wet curing room is maintained at 5˚C or higher.
- Products that completed the wet-curing should be transferred to the yard and cured naturally until the shipment in the 28th day. During storage, care should be taken to prevent the products from being affected adversely.
Product Testing
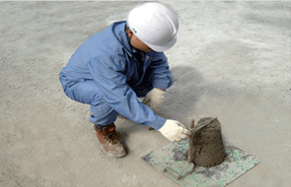
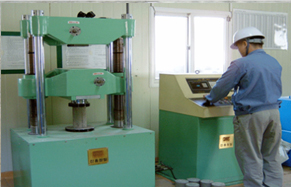
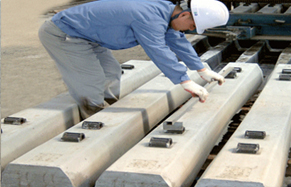
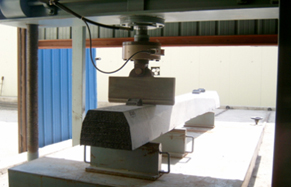
Slump Test
Before the concrete placement, slump test should be performed in accordance with KS F 2402(method for slump test of Portland cement concrete) to determine the conformity.
- The slump test should be performed by the daily quantity of concrete placement once in the presence of supervisor. (Limit the slump to 5.5-10.5cm)
Air Volume Test
For the air volume test, check the fluctuation of air volume in accordance with KS F 2409, KS F 2421, etc., and adjust the mixing ratio of concrete if necessary.
- Air volume test should be performed by the daily quantity of concrete placement in the presence of supervisor. (Limit the air volume to 2-5%)
Chloride Test
(A) Chloride test should be performed of fresh concrete before concrete placement. Chloride content should be calculated by multiplying the ion concentration of uncured concrete by the unit quantity set forth in the Mixing Specification.
Chloride content measurement test should be carried out at least once per concrete placed daily and whenever the mixing ratio is changed.
- Chloride test should be performed once by the daily quantity of concrete placement in the presence of supervisor. (Limit the chloride content to 0.3kg/㎥ or less.)
Compressive strength test
(A) For the compressive strength test of concrete, the specimens should be made in accordance with the KS F 2405 and KS F 2404 for the specimens.
- The compressive strength should be tested and maintained at 38-42 Mpa before prestress introduction.
Appearance Test
The surface should be smooth and of good quality and free from defects such as twist, unevenness, surface defects, cracks, and twisting of the rail bearing surface.
- Only products that passed the test should be released after the whole quantity inspection performed in the presence of supervisor in all cases of demolding and shipment.
Dimensional Inspection
The shape and dimensions of the Tie shall be inspected according to the shop drawings. For the measurement of major parts requiring accuracy, the dimensional inspection should be carried out by using the measuring instruments, made separately, with prior approval of supervisor.
- Whenever demolding is performed, only the products that passed the whole quantity test should be cured in the presence of supervisor.
Performance Test
The compressive strength of concrete at the age of 28 days should meet or exceed the level specified in the shop drawing based on the results of test performed in accordance with KS F 2405.
- The test should be performed once by the daily quantity of concrete placement. (50Mpa or higher)
The compressive strength of concrete at the age of 28 days should meet or exceed the level specified in the shop drawing based on the results of test performed in accordance with KS F 2405.
- The test should be performed once by the daily quantity of concrete placement in the presence of supervisor. (1 spot at the center; 2 spots in the lower part)
- The compressive strength should be maintained at 53KN or higher at the center and at 155KN or higher in the lower part.